We’re making another keyboard, and other news
TL;DR:
1. Lots of things are in stock:
- Keyboards! https://shop.keyboard.io/
- Solid black keycaps! https://shop.keyboard.io/products/model-01-keycaps-black
- Travel cases! https://shop.keyboard.io/collections/model-01-accessories/products/model-01-travel-case
2. We got some of our tooling back!
3. Chrysalis is officially out of alpha!
4. We’re making another keyboard!
Hello from Oakland,
In June, we ended things on a bit of a cliffhanger about negotiations with our old factory. Below, you can read the next chapter in that saga. But first, we have a bit of exciting news to share.
We’re making another keyboard!
The Keyboardio Atreus
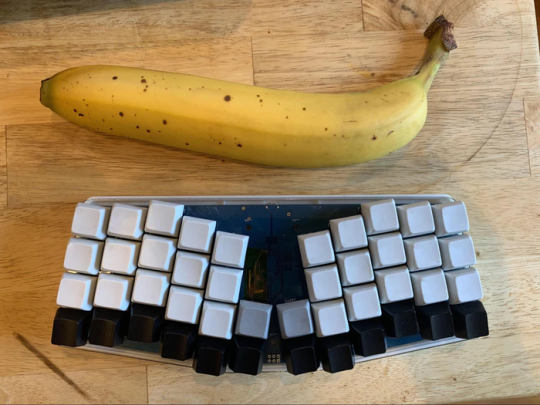
An early prototype of the Keyboardio Atreus co-developed with Technomancy, presented with a banana, for scale. (The shipping product will have different keycaps and a black plate and enclosure.)
Over the past few months, we’ve been putting together our first official collaboration.
We’ve long been fans of the Technomancy Atreus, a minimalist ergonomic keyboard that shares much of its DNA with the Model 01. It’s an open keyboard design. Folks in the community frequently build themselves an Atreus with nothing but a laser-cutter, an Arduino, and a handful of switches.
Earlier in 2019, Phil Hagelberg, the Atreus’ creator approached us to do a design review of an update to the Atreus’ circuit board he was considering. We got to talking and realized that we might finally be in a good position to do more than just review his design.
Over the summer, we did a ground-up redesign of the Atreus’ circuit board to improve quality and reduce costs. (The only change to the key layout from the original Atreus is that Phil snuck in another couple keys.) From there, we started talking to potential keyboard factories.
We’ve selected the factory we’ll be working with. They’ve helped us design a sturdy ultra-minimalist tray-style enclosure. It makes the classic laser-cut Atreus look…big.
Our goal with the “Keyboardio Atreus” is to offer a fully assembled keyboard at an attractive price. The keyboard will run Kaleidoscope and be customizable with Chrysalis. (It’s based on a Microchip ATmega32U4, so should also be able to run other keyboard firmware like QMK.)
The Keyboardio Atreus will ship with MX-style switches in hot-swap sockets, so you’ll be able to swap keyswitches without soldering.
We expect to open presales for the Keyboardio Atreus within the next couple months.
If you think you might want an Keyboardio Atreus, please join the waitlist: http://eepurl.com/gFN1nL
Chrysalis graphical keyboard configuration tool
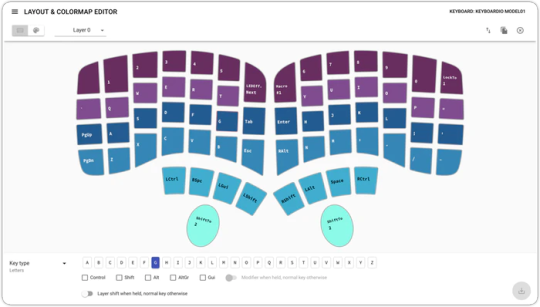
It’s been quite a long time coming, but we’re finally ready to announce the beta release of Chrysalis, our graphical configuration tool for keyboards running Kaleidoscope.
Chrysalis makes it easy to change your keyboard’s layout and LED color schemes without editing text files or compiling anything. It also has built-in functionality to help you update your keyboard’s firmware to the latest version.
Chrysalis runs on macOS, Windows, and Linux.
You can see an example of editing your keymap with Chrysalis here: https://github.com/keyboardio/Kaleidoscope/wiki/Edit-keymap-with-Chrysalis
You can download the current beta, v0.6.2 at https://github.com/keyboardio/Chrysalis
Upcoming features include display of non-ASCII key layouts and the ability to build macros from within Chrysalis.
What happened next
When we last wrote, our old factory had definitively refused to give us our tooling, our inventory, and to return the money we’d paid for things that hadn’t been delivered.
They said that they didn’t want to return our tooling because they believed that if they did, we wouldn’t place another order with them. We were very clear that we would never place another order with them and that it was a choice between returning our tooling and us filing a lawsuit, but that didn’t seem to make much of an impact on them.
We left you on a bit of a cliff-hanger, though it should come as no surprise to anybody that the next thing we did was to file a lawsuit against them in the Chinese courts.
Apparently, one of the options available for a contract lawsuit in China is for the court to appoint a mediator to try to resolve the issue without time and expense of a trial. Our lawyer recommended that we try mediation first and we agreed with her.
It took a few months for the court to appoint a mediator and a good bit of time after that for everybody to sit down for a first mediation session.
Because negotiation is ongoing, we can’t yet talk much about the process, though we may be able to in the future. (There are some good stories.)
One of our top priorities has been to get back enough of our tooling to make the keycap sets we owe you.
At a certain point in the mediation, the mediator brought in the judge to help expedite things. The judge…suggested that the factory turn over all of our tooling and any inventory the factory wanted credit for right away, as that would help make the rest of the mediation a good deal simpler. (Once it’s “just” about money, it’s a lot easier for the court to evaluate.)
At the last minute, the factory told our lawyer and the judge that they weren’t going to give back all of our tooling, just…most of it. They had some explanations, but they didn’t really make any sense.
Way back in May, we’d signed a “tooling custody” contract with another keyboard factory used by some of our friends. The idea was that once our old factory agreed to release our tooling, this other factory would pick up the tooling, inspect it, test it, and hold onto it for us. As part of a separate contract, they’d also produce new keycap sets for us.
In early September, the new factory sent a truck to the old factory to pick up everything they could.
To our great surprise, they actually got back most of our tooling.

They got the baseplate tooling.
They got the stand tooling.
They got the rail tooling.
They got the center bar tooling.
They got the keyplate tooling.
They got the rubber foot tooling.
They got the wave soldering jigs.
They got the PCB testing jig.
They got the keycap painting jig tooling.
They got the keycap tooling.
They didn’t get the tooling for the plastic package for keycap sets.
They didn’t get the keycap “transfer” tooling, used to move the keycaps from the injection molding machine to the painting jigs.
More on those a bit later.
They were also supposed to pick up around 1300 sets of unpainted, black, and QWERTY keycaps which we knew to be sitting in the old factory’s warehouse.
Initially, the old factory said that there must be some mistake, as there were no keycap sets in their warehouse, but the mediator made a phone call and resolved that issue.
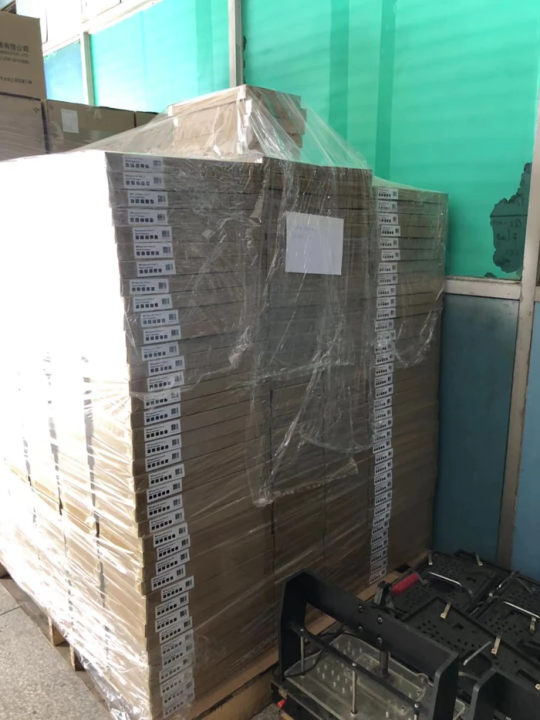
The new factory got about 600 sets of black keycaps, packaged and ready to ship. Those are now in our Hong Kong warehouse, ready to send out to folks who order them. (This is a little odd, because it’s actually -more- of those than we’d ordered.)
They also got another 800 or so sets of unpainted keycaps (without UV coating) still on the painting jigs and we expect to be able to use those to partially fill the orders for Dvorak, Colemak, and Linear A.
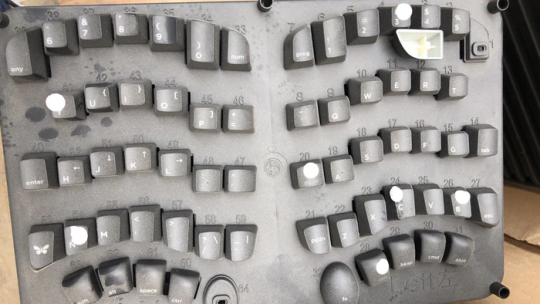
This set didn’t pass QC
The old factory also offered up about 1000 more sets of QWERTY keycaps which had failed quality control checks some time in the past, but the new factory declined to take those.
A new era
Over the course of the past few weeks, we’ve been working with the new factory to test all of the tooling and to formulate a plan to produce Dvorak, Colemak, and Linear A keysets, as well as some extra QWERTY and unpainted sets.
The plan was that the new factory inspected the injection molding tools one by one and then set them up on molding machines to make sure they worked, as well as to dial in materials, temperature, and cycle times.
Western friends with decades more manufacturing experience than we have warned us that things might not go smoothly. In their experience, it was nearly unheard of for injection tooling designed for use on one machine type at one factory to “just work” when transported to another factory and set up on another type of injection molding machine.
We’re happy to be able to report that our friends’ worries were largely unfounded.
Tooling tests finished up on the 27th.
The baseplate tooling was fine:
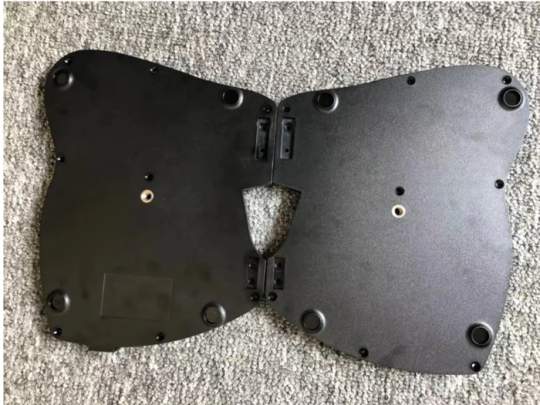
The stand tooling looked great:
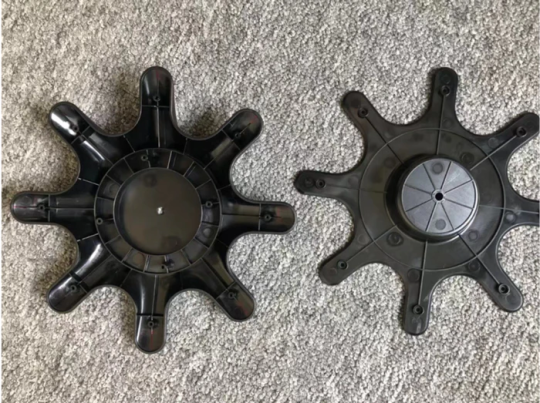
The rail tooling worked perfectly:
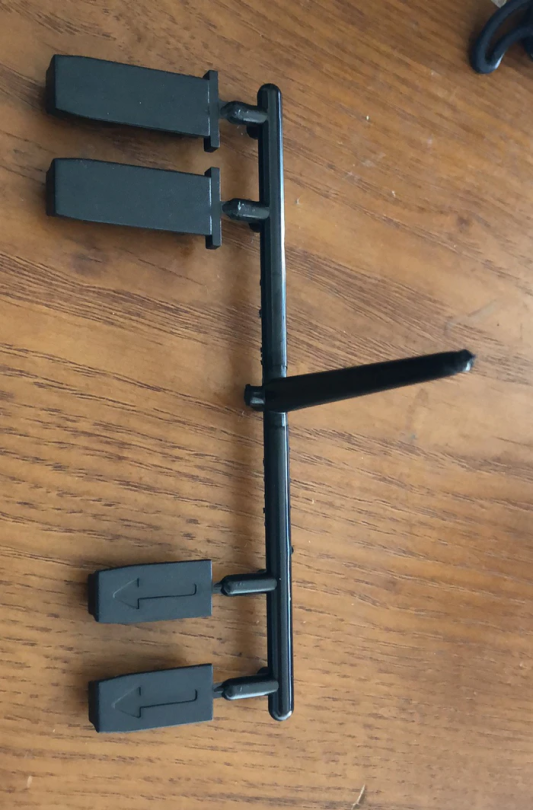
The center bar tooling had a small nick at one end, but that should be possible to fix up pretty easily. We did discover that the center bars produced by the old factory weren’t made with glass-filled nylon as we’d been promised, but had, instead, been made out of a mix of ABS and polycarbonate, like the stands and baseplates. After some testing, the new factory told us that they found the ABS+PC mix seems to be a better fit for these parts, so we’re just rolling with it.
We didn’t test the keyplate stamping tooling or the rubber foot tooling, but that’s inexpensive and would be pretty easy to repair or replace.
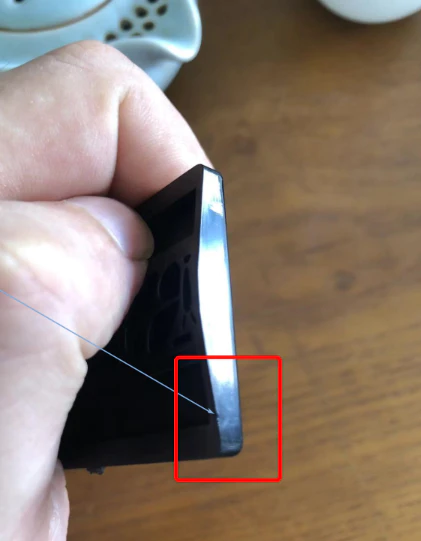
Nick in the center bar due to damaged tooling
We also haven’t tested the keycap painting jig tooling, but aren’t too worried about it.
The very last tool to get tested was the keycap injection tooling.
The old factory outsourced keycap injection molding to one supplier, keycap painting (and UV-protectant coating) to another supplier, and keycap laser engraving to a third supplier. The new factory does all of these things in-house.
The first thing that the factory discovered when getting ready to test the keycap injection-mold tooling was that the existing keycaps, which were supposed to have been made from a mix of ABS and polycarbonate just…weren’t. They’re ABS. They discovered this when trying to inject a sample set of keycaps out of ABS and polycarbonate. When melted, ABS will “flow” through a mold much more easily than polycarbonate will. The mold just wasn’t designed to let enough plastic flow through into all the keycaps when there was polycarbonate in the mix. In fact, the “normal” ABS material the factory used didn’t even flow well enough to inject full sets of keycaps. They had to switch to a formulation of ABS designed to flow better in stubborn molds.
We’re going to roll with the punches and use the factory’s recommended ABS formulation going forward. Adding polycarbonate to ABS makes it stronger, but can make it more brittle. It can also change how much light shines through the plastic. We have, as yet, had no reports of a Model 01 keycap’s plastic breaking. Because our keycaps are painted, the plastic inside doesn’t really matter a whole lot in day to day usage. When you’re typing on a Model 01, your fingers never touch the plastic. They’re touching the clear UV-protectant coating on top of black paint.
In the end, the new factory figured out a plastic type, pressure, temperature, and cycle time that produced workable keycaps. And that’s where they ran into the problem alluded to earlier. The old factory never handed over the keycap transfer tooling, despite having charged us for it.
In an earlier backer update, we showed you this video of how keycap sets were molded and moved from the injection molding machines to the painting jigs. It does clever things with vacuums and razors to pull all of the keycaps out of the mold and get them onto the painting jigs with minimal human involvement.
Well, without that magic tool, things do not go so smoothly.
The new factory advised us against creating new transfer tooling for now: it’s relatively expensive and time-consuming to make, and we’ve been considering remaking the keycap tooling in the future. (As you might guess from the number of manufacturing issues we’ve had with the keycaps, this tooling was not terribly well designed.)
As they were doing the injection tests, the factory hit upon a decidedly low-tech solution for getting full keycap sets out of the molding machine:
When we commented that this seemed to be a very labor intensive way to get a set of keycaps out of the mold, the factory said that for production, they’d ordered extra-wide tape.
Once the injection molding machine got dialed in, the factory sent us some photos showing how the light shines through the new keycaps.
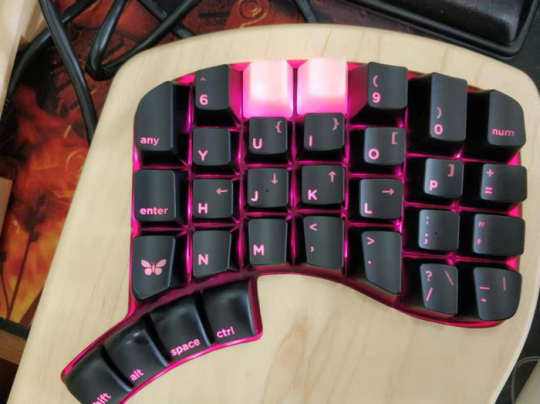
In the picture above, one of the unpainted keycaps is from the old factory and the other is from the new factory. They transmit very, very similar amounts of light. If anything the new ones actually let through a bit more light.
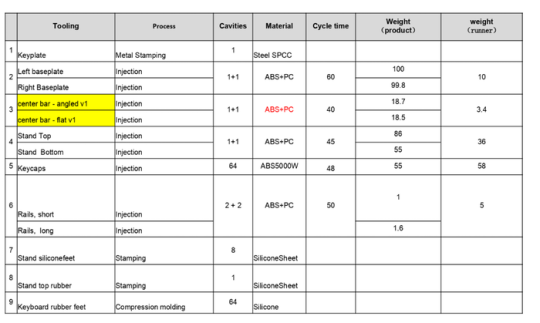
As mentioned earlier, the old supplier hadn’t turned over the tooling for the plastic packaging for keycap sets.
We ended up needing to have new keycap packaging tooling made. Last time around, this was a three month process that, we were told, took multiple suppliers before we got something usable.
Our old keycap packaging:
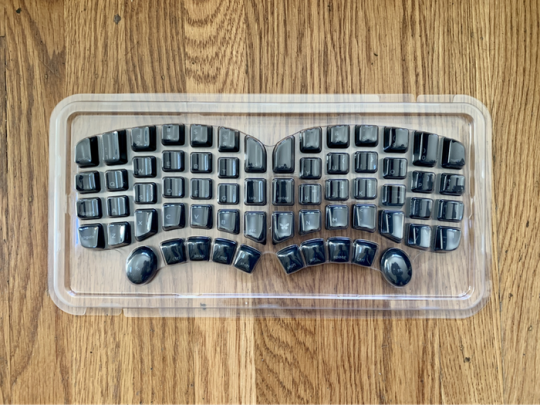
The old packaging was a little bit bulkier than we wanted, which led to slightly higher shipping charges than we’d planned for. We asked the new factory to try to make the new packaging smaller than an A4 sheet of paper and suggested that they consider rotating the left and right hands’ keycaps. They managed to put together a design that came in a few mm under an A4 sheet.
This time around, once we’d agreed on a design, it took a week to get to a first sample out of the tooling:
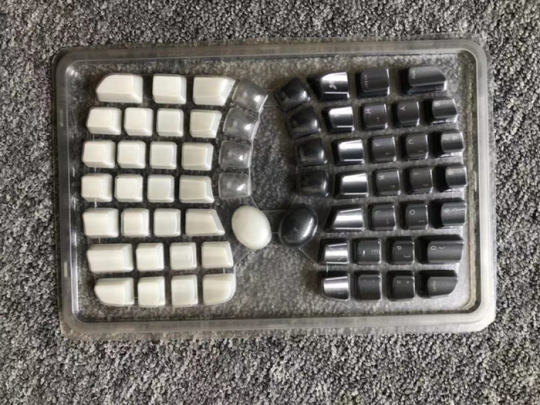
Right now, most factories in China are closed for the Golden Week holiday. Next week, the new factory expects to get us a full quotation for keycap sets, along with an estimated lead-time.
Once we get the pricing and lead-time figured out, we’ll let you know, either with a full backer update, a comment on this post, or some tweets as @keyboardio.
Before we ship out any keycaps, we’ll be in touch by email to ask you to confirm your current address.
Keyswitch issues
We’ve had a handful of reports of mechanically failed keyswitches on keyboards either near the end of their one year warranty period or after their warranties have expired. In one case, an unlucky customer has run into two failed switches.
The hallmarks of a failed switch are a key that either never generates keypresses or never stops generating keypresses once it starts. The switches we’re using are rated for 50 million keypresses, or 1.5 years of hitting a key every second, so we were a bit surprised. We’ve been working with our keyswitch supplier to find a root cause and even delivered samples of the failed switches directly to the general manager of their manufacturing partner for lab analysis, but haven’t heard results from their side.
We’ve been providing customers affected by this issue with two options for remediation:
1) If you’re not comfortable with a soldering iron, we’ll perform the repair in California, at no charge for parts or labor, even if your warranty has expired. (If your warranty has expired, we’ll ask you to pay the return shipping.)
2) If you or someone near you is handy with a soldering iron, we’re happy to send you a few replacement switches. If your warranty has expired and you’re outside the US, we’ll ask you to cover the shipping for the keyswitches.
If you’re running into this issue (or any other issue), please don’t hesitate to email us at help@keyboard.io.
While we can’t promise that we’ll be able to continue to offer free repairs or free replacement switches for out-of-warranty keyboards perpetually, we’ll keep doing it as long as we can.
Model 01 Stock
Moving to a new supplier and having to redo some of our tooling is a natural time to look at the Model 01’s design to see what, if anything, we might want to update. We’re deep into that process, but don’t currently know when we’ll have anything to announce on that front.
We have enough Model 01s in stock to last for a little while, but aren’t yet set up to produce new butterfly-shaped keyboards at the new factory. There is a chance that we’ll run out of stock before new keyboards are on the assembly line.
If you think you’re going to want a Model 01 in the near future, now is a great time to order it from https://shop.keyboard.io.
Note: originally, this post referred to the "Keyboardio Atreus" as "the Atreus 2". This was confusing to some people who read this post after we renamed it, so we've edited it since posting.